数控冲床加工时注意事项
数控冲床加工时的注意点:
(一)冲孔的最大孔径及吨位
例如:板厚6mm.cD88.9mm的板能不能冲切,不能凭空想象估计,它是由冲压能力来确定的,一般冲孔所需的压力由下公式求得:
P=A×t×t
P一冲压力(kg) A-所冲孔的周长(mm)t一板厚(mm)T一材料剪切强度(kg/mm)
如武汉众能科技有限公司生产的VT-300冲床冲6mm热轧板,最大加工
孔径为:
30 x1000=3.14 x D x 6 x 42
D=cl,37.9 (mm)
所以说在数控机床上冲6mm热轧板最大能冲cP37.9mm的圆,超过此数值就必须用其它方法来实现了,如小圆模步冲的方法。
(二)注油润滑
注油量和次数由加工材料的条件而定。无锈无垢的材料,要给模具注油,油用轻机油。有锈有垢的材料,加工时锈会进入模具和外套之间,跟契子一样,使凸模不能自由移动。这种情况下,如果上油,会使锈垢更容易沾上,因此冲这种材料时,相反要把油擦干净,每半月要把模具分解一回,用汽油洗干净,重新组装,这样就能进行令人满意的加工。高速数控冲床模具必须严格进行保养,定期用轻机油对卸料套、注油口、模芯本体与卸料套的接触面、凹模进行润滑,这样可延长模具的使用寿命。但是过多的润滑油往往会滞留在上模端面,冲切时的打击容易使上模端面与废料之间产生真空吸附作用,形成垫渣,即:废料反弹。遇到这种情况,应将板材的油垢清理干净,并保持模具的干净,不要加注过量的润滑油,即可进行顺利的冲切。开。
(三)带料及废料反弹
冲头带料及粘连是指在正常情况下,上模芯与板料不能及时脱开或完全脱不
1、带料的危害性:
(1)会使模芯损坏或折断。
(2)会损坏夹钳以及损坏板料产品,卷曲的板材甚至会撞坏护罩。
2、引起带料的原因:
(1)模具弹簧疲劳失效或断裂。
(2)入模量过大。
(3)模具导套与模芯滑动阻力大。
(4)所需退料力大于弹簧力。
(5)送料速度过快,弹簧响应不够或不灵敏。
(6)材料积屑瘤。
(7)废料反弹。
(8)模具间隙及精度等其它原因。
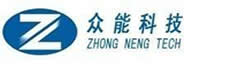
3、带料的解决方法:
(1)根据样本及其它试验数据来看,弹簧预期寿命为50万次,有时在恶劣的条件下还会更短,到时弹簧会疲劳而失去应有的弹性,弹簧会明显缩短甚至断裂,必须及时向可信赖的模具供应商订购新弹簧。
(2)入模量应控制在l-2mm之间,过深会造成模芯的脱模行程和阻力加大,从而延长了弹簧的反应时间,模芯未完全从板料中退出即送料,可能损坏模具、板材或夹钳等。
(3)当滑动面上有过多的灰尘及其它脏东西或缺油时,会使滑动阻力变大,抵消了一部分弹簧力,就可能引起带料,此时应将模具拆洗,加润滑油,改善润滑条件。
(4)推料力大于弹簧力主要是指冲压吨位大,有几种可能性,一是刃口严重钝化,需额外的吨位,而且切断面粗糙及毛刺增大,产生很大的抵抗力,此时应及时刃磨;二是模具间隙与板材不匹配,当模具间隙偏小时会使材料抱紧凸模,此时应选择与板材匹配的下模或研磨下模使其间隙变大;三是当模具规格接近极限工位尺寸同时板料较厚时,所需退料力大于弹簧力,此时需将其往上跳一级工位或选用重载弹簧。
(5)当高Cr模具材料与高Cr冲压板材(如lCr13等不锈钢)连续冲裁时,温度会升高而产生亲和力,相当于一对相同的摩擦付,极易磨损刃口或产生积屑瘤,所以当冲不锈钢时推荐使用进口高速钢,而不能使用国产高Cr材料,如Cr12MoV等,此外,冲压时会常遇到带附膜的不锈钢,此附膜既薄又韧,与板材粘贴松散有分离现象,冲切时易产生带料,这种情况下一要选用刃口锋利的进口高速钢模具,二是要将有附膜的一面放在下面,使附膜位于剪切层附近以达到被完整切下的目的,但这样做应充分考虑毛刺面对零件的影响。
(6)废料反弹也是造成带料的重要原因之一,废料反弹后废料如果有一半在下模处,会造成冲双料的现象,使模具严重偏载和吨位加大,从而引起带料或模具的损坏。
(7)最后还有一点就是模具本身制造精度及机床模位对中精度问题,也可能引起带料,此情况发生时应选用正规专业数控模具厂家制造的模具以及用校棒校正机器模位。
4、废料反弹:
废料反弹指冲孔废料未能从凹模洞口顺利排出,反而反弹到凹模端面或零件毛坯表面上的现象,此弹发的废料也称为垫渣。
5、废料反弹的危害性:
(1)当冲模在垫渣附近继续冲切时,卸料导套会将垫渣击入板料表层,导致零件因尺寸与表面质量不合格而报废。
(2)垫渣落在下转盘上使送料存在隐患,板材会被划伤甚至撞坏。
(3)有时因连续产生垫渣致使垫渣重叠超m模具强度极限而损坏模具,单件或小量生产较多时,凶垫渣导致的报废率就显著的提高。
(4)垫渣有一半在下模口处时冲击,会引起带料。
6、引起废料反弹的原因:
(1)模具自身的原因
a.间隙是否合理 b.刃口是否锋利
c.模具入模是否适中 d.润滑是否有利
(2)材料状态的原因
a.材料表面状态是否良好 b.材料附着层方向是否有利于冲击
(3)程序编制的原因
a.模具选择 b.冲切顺序与方向
c.冲击尺寸的确定
7、废料反弹的解决方法:
(1)下模间隙偏大会使废料向上翘曲,使得其与凹模内表面的接触面积减少,磨擦力更小,在高速冲的状态下会出现废料反弹,所以针对间隙过大的情况,一定要选择合适的间隙,有时甚至可以考虑使用较小一点的间隙。
(2)刃口锋利的模具冲击次数达到一定次数后,刃口边缘像霜一样发白而且变圆,这都是加工硬化和钝化造成的,在这种状态下加工会使废料对凸模刃口边缘的包容现象越来越明显,极有可能随上模的返回而一同带出凹模,遇到这种情况必须立即刃磨刃口,刃磨后必须用退磁器进行消磁。
(3)上模刃口直径或宽度在9mm以上的采用聚胺脂退料钉,宽度在8mm以下,大工位细长模具采用2。斜刃口,能有效的防止废料反弹,但聚胺脂属于易损件,所以用户在使用过程中应每星期进行检查并及时更换,可以向模具生产厂家直接订购,斜刃口应在刃磨后仍保持斜刃口,不能因为没有设备或怕麻烦而将其磨成平刃口。
(4)入模量应控制在l-2mm之间,过浅会造成废料不能完全剪断,在送料时废料会随着板材的移动而被带出下模,在这里就涉及到模具刃磨量的问题,如模具刃磨超过4mm后就必须考虑换模芯了,否则凸模对凹模的伸入量会越来越少,同时冲击时作用于板材上的能量会增加,从而引起板料产生较大的翘曲,这方面原因会增加废料反弹的产生机会。
(5)下模刃口深度过高时,会造成废料重叠,废料间的空气压缩后,上面的废料会随冲头回程而弹出下模,标准的下模刃口深度应为入模量、料厚、刃磨量的总和。
(6)上下模或上下模位严重偏心时,单边过大的毛刺同样会使废料随板材的移动而被带出下模。
(7)上模底部或板料上一般不可避免有点涧滑油或防锈油,但决不可多到形成流体,冲击时容易使上模端面与废料之间产生真空吸附作用,形成废料反弹,遇到这种情况需将上模或板料上的油擦掉。
(8)板料的附者层也是引起废料反弹的重要因素之一,跟解决带料一样,需选用刃口锋利的模具,同时应将附着层的一面放在下面。
(9)高速数控转塔冲床应用之所以越来越广泛,一个很重要的原因是它具有拼接冲切的柔性加工特点。虽然如此,在编程时不要图省事随意选择模具。针对某一型孔的特点,首先选择能一次完成型孔的模具,须拼切加工时,应选用最小拼切废料最大、最接近模具尺寸的模具。若最小拼切废料太小,模具间隙较大时废料不易被冲切掉,即使废料被冲切掉入凹模,若滞留在前次废料之上,很容易因振动反弹跳出凹模,形成废料反弹,所以要一定科学地选用模具。
(10)除此之外,还有冲切顺序、方向及尺寸等多方面因素,都能引起废反弹,只能靠生产一线操作技术人员不断加工实践、总结,才能最大限度地排除引起废料反弹的各种不利因素。以上分析,参照了有关资料并结合了我公司技术研究人员多年研制、操作经验而总结出来的,肯定有不全之处,广大数控冲床用户在生产实践中肯定还会发现其它引起带料和废料反弹的原因,以及更好地解决这些弊病的措施,望不吝指教!总体来说,引起带料和废料反弹的因素很多,我公司在模具结构及模具制造新工艺面不断改进的同时,售后服务部门也加强了对用户操作人员的技术培训,要知道没有一个经验丰富的操作人员就不可能将机床、模具用好,也就是说操作人员经验越丰富故障越少。
更多访问:http://www.zntech.net/
数控冲床加工时注意事项
|